Oxy-acetylene gas welding, also known as gas welding, is a widely used welding process that makes use a flame produced by the combustion of a mixture of oxygen and acetylene gases to heat and melt the metal being welded. The flame is directed onto the metal, and as the metal melts, a filler rod is added to the joint to create the weld. This process has been around for over a century and is still widely used today due to its versatility, portability and low-cost.
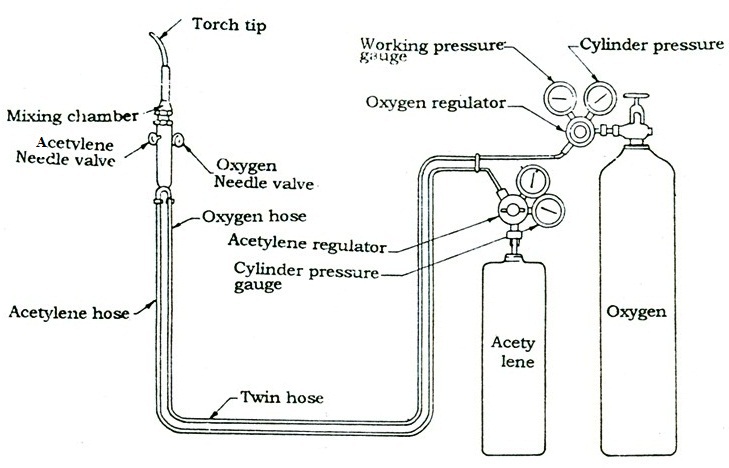
One of the key advantages of oxy-acetylene gas welding is that it can be used to weld a wide range of metals, including steel, aluminum, brass, copper and cast iron. The process is relatively low-cost and easy to set up, making it a popular choice for small-scale welding projects such as automotive repairs, metal fabrication, and metal art.
The process has a high heat output and a large flame, which makes it well suited for welding thick sections of metal or for creating large welds. The flame can be adjusted to suit the thickness of the metal and the type of joint being welded, allowing for precise control and a high-quality weld.
However, the process also has some limitations such as the need to constantly monitor and adjust the flame, the risk of explosion or fire if not handled properly, the need of a constant supply of oxygen and acetylene gases, and the potential for warping or distortion of the metal due to the high heat.
Additionally, the process generates heat, smoke and fumes, which means that proper ventilation and personal protective equipment are required to ensure the safety of the operator. Welders should always wear protective clothing, including a welding mask, gloves, and a protective apron, and work in a well-ventilated area to avoid inhaling harmful fumes.
To set up for gas welding, a welding torch is connected to an oxygen and acetylene gas cylinder. The torch has two valves, one for oxygen and one for acetylene. The welder adjusts the mix of gases to get the right flame for the job. In general, the oxygen is adjusted to get the right temperature to melt the metal, and the acetylene is adjusted to get the right size of flame for the job.
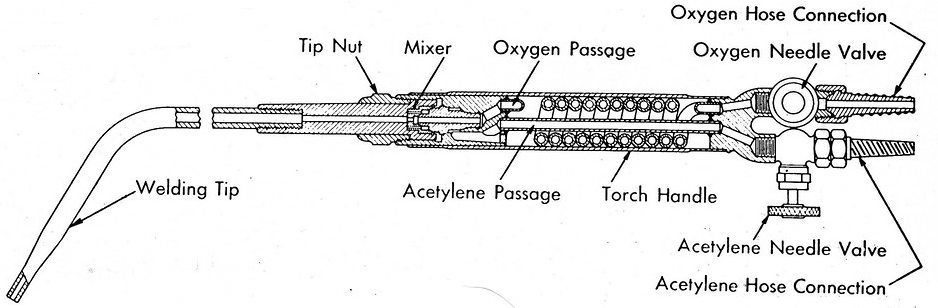
Oxy-acetylene gas welding is a widely used and versatile process that can be used for a variety of welding applications. However, it requires proper handling, safety precautions and knowledge of the process to achieve good results.
Filler Rod Used in Oxy-Acetylene Gas Welding
When using the oxy-acetylene gas welding process, the filler rod used is typically made of the same material as the base metal being welded. The filler rod is added to the joint as the metal melts, and it serves to fill in any gaps in the joint and to add strength to the weld.
Some of the most commonly used filler rods for oxy-acetylene gas welding include:
- Steel filler rods: These are used for welding steel and are available in various types, including low carbon steel, mild steel, and high carbon steel.
- Aluminum filler rods: These are used for welding aluminum and are available in various types, including 4043 and 5356.
- Brass filler rods: These are used for welding brass and other copper alloys.
- Cast iron filler rods: These are used for welding cast iron and are available in various types, including nickel-based and high-chromium filler rods.
It’s important to use the right filler rod for the specific metal you’re welding to achieve the best results. Improperly matching the filler rod can lead to weak or porous welds. Additionally, the filler rod must have a similar composition as the base metal to avoid cracking, brittleness or other issues.
It’s also important to note that some filler rods are designed to be used with specific types of gas welding, such as TIG or MIG welding, and are not suitable for use with the oxy-acetylene process.
Welding Technique
The welding technique for oxy-acetylene gas welding involves several steps:
- Set-up: The welding torch is connected to an oxygen and acetylene gas cylinder. The torch has two valves, one for oxygen and one for acetylene. The welder adjusts the mix of gases to get the right flame for the job. In general, the oxygen is adjusted to get the right temperature to melt the metal, and the acetylene is adjusted to get the right size of flame for the job.
- Preheating: Before beginning the weld, the welder preheats the metal by directing the flame onto the metal in the area where the weld will be made. This helps to remove any impurities or contaminants and to bring the metal up to the proper welding temperature.
- Welding: The welder begins the weld by directing the flame onto the metal at the start of the joint. The flame melts the metal, and the welder uses the filler rod to add metal to the joint. The welder moves the flame along the joint, keeping the filler rod in contact with the metal to create the weld.
- Cooling: After the weld is complete, the welder allows the metal to cool before handling it. This helps to prevent warping or distortion of the metal.
It’s important to note that the welding technique for oxy-acetylene gas welding requires a certain level of skill and experience. It’s also important to use proper safety precautions, including wearing appropriate personal protective equipment, such as a welding mask, gloves, and a protective apron, and working in a well-ventilated area to avoid inhaling harmful fumes.
As for the flame, the welder should be able to adjust it to get a neutral flame, which is a flame that burns clear and has a light blue inner cone and a dark blue outer cone. This is the most suitable flame for welding, as it provides the right temperature and size of flame for the job.
Additionally, the welder should keep the flame moving constantly, to avoid overheating or burning the metal, also the welder should use the right size of flame for the thickness of the metal and the type of joint being welded.
Chemical Reactions Involved
The chemical reactions involved in oxy-acetylene gas welding are the combustion reactions between oxygen and acetylene gas.
When oxygen is mixed with acetylene gas and ignited, the oxygen reacts with the acetylene to create heat, light, and various byproducts. The primary chemical reactions involved are:
Oxygen and Acetylene Combustion:
The main chemical reaction that takes place is the combustion of acetylene (C2H2) with oxygen (O2) to form carbon dioxide (CO2) and water (H2O).
[su_note note_color=”#fbfbfb”] [latex] 2C_2H_2 + 5O_2 \longrightarrow 4CO_2 + 2H_2O + heat [/latex] [/su_note]
Acetylene Decomposition:
Another chemical reaction that can happen when the acetylene flame temperature is too high, is the decomposition of acetylene into its constituent elements, carbon and hydrogen. This reaction is called “decomposition” because the acetylene breaks down into simpler compounds.
[su_note note_color=”#fbfbfb”] [latex] C_2H_2 \longrightarrow 2C + H_2 [/latex] [/su_note]
This decomposition reaction releases large amounts of heat, which can cause the metal to overheat and burn. This is why it’s important to use the correct flame size and temperature when welding with oxy-acetylene.
The chemical reactions involved in oxy-acetylene gas welding are exothermic, meaning they release heat. This heat is used to melt the metal, allowing the welder to create a strong, continuous weld.
It’s also worth noting that when welding, the metal also reacts with the oxygen in the air, this reaction is called oxidation, and it can cause rust, discoloration and weaken the welded joint if not controlled properly.